Battery
Viscosity and density quality control in battery production slurry mixing and coating lines
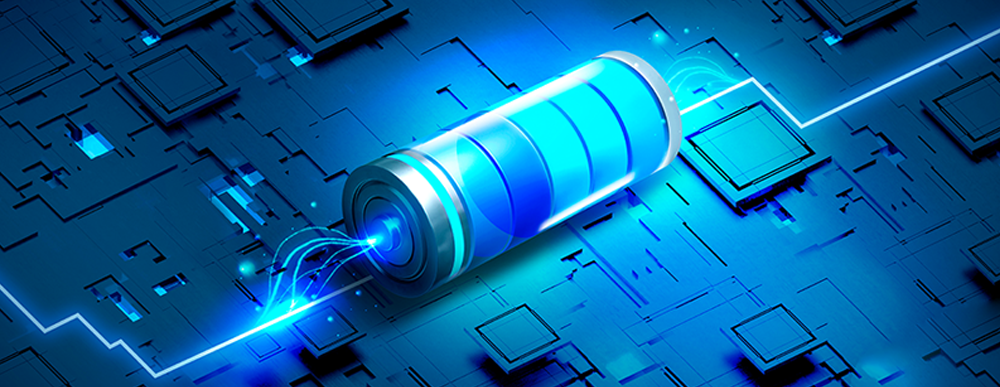
The production of batteries involves depositing a slurry containing active materials, conductive materials and solvents and polymer binders onto a copper film or aluminum film. This is followed by drying, calendering and resizing of the electrodes.
Slurry is a very complex suspension system containing many solid particles of different chemicals, sizes and shapes in a high viscosity medium. Thorough mixing of the slurry is essential for homogeneity. The rheological properties of a slurry affect important properties such as slurry stability, ease of mixing, and coating performance, as well as the finished electrode. The composition and applied processing conditions can affect the rheology of the slurry.
Density and viscosity quantify flow properties and characterize the degree of structure within a sample and the extent to which solid- or liquid-like behavior dominates. The viscosity of the slurry is particularly important in the electrode manufacturing process and plays an important role in battery manufacturing processes such as coating. The viscosity of the polymer binder solution affects coating performance. It affects the ease with which the powder is dispersed within it, the force required for mixing and the speed of application of a uniform coating.
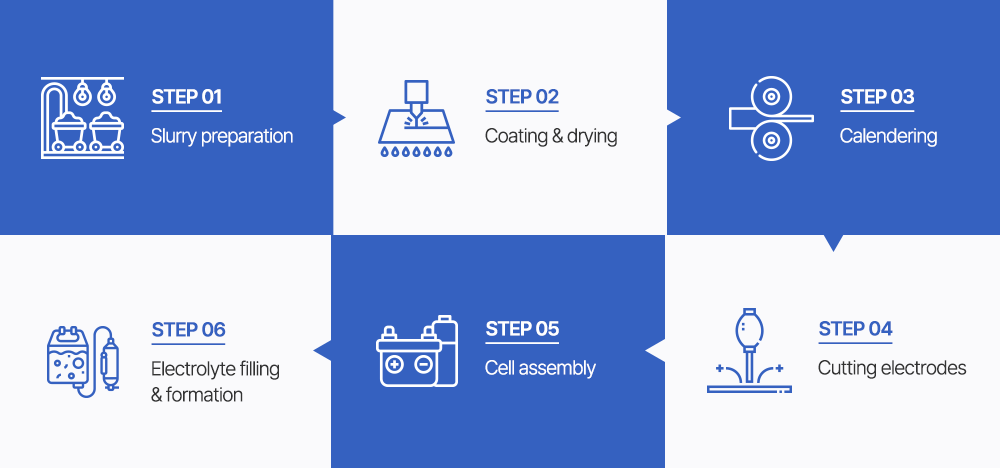
In order to maintain quality to improve battery performance and lifespan, the entire battery manufacturing process must be optimized through close monitoring of viscosity and density.
▶ Optimize batch processes with control of density and viscosity | ▶ Uniformity control of coating thickness and layer density |
▶ Monitoring and process control of continuous mixing processes | ▶ educe battery manufacturing time by optimizing all processes |
▶Significantly reduce material costs by maintaining consistency and quality in the slurry manufacturing process |
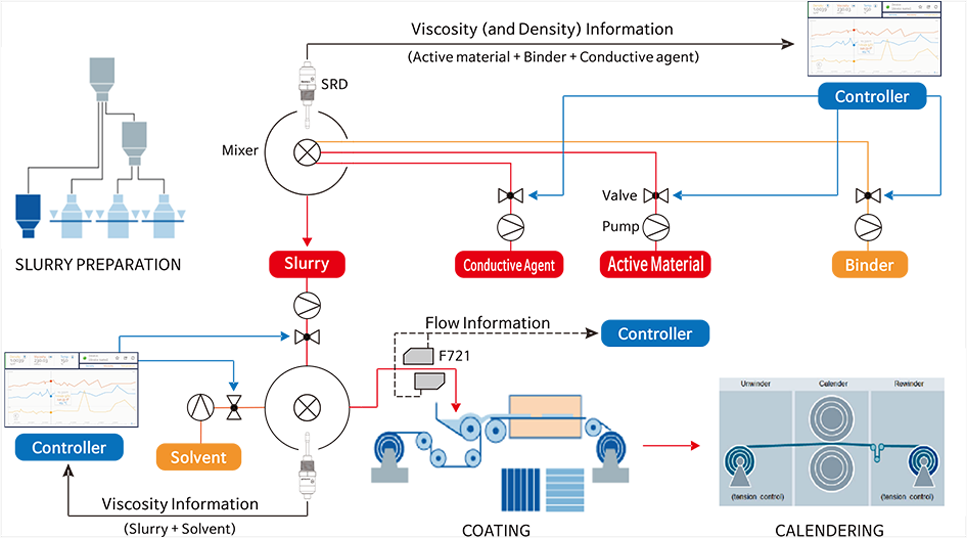
< hy measuring viscosity is important >
Viscosity (and rheology) are the most important parameters in adhesive production and processing. | arious solvents, dissolvable agents, resin powders or inert fillers control the viscosity of the adhesive. | The viscosity of adhesive systems increases or decreases depending on application and operating environment. |
It is highly desirable for the viscosity to be automatically adjusted to a substantially constant value. | Essential for improving performance and reducing costs in virtually all formulations and delivery processes | Recognizing the need for a viscometer to monitor viscosity and temperature |
Ensure consistency using temperature compensated viscosity as key process variable | Breakdowns can be reduced |
Brookfield TT-100 | ||
![]()
|
Rheonics SRV, SRD | ||
![]()
|
Brookfield TT-100 | ||
![]()
|