Viscosity management of automotive and PCB production adhesive and sealant formulations
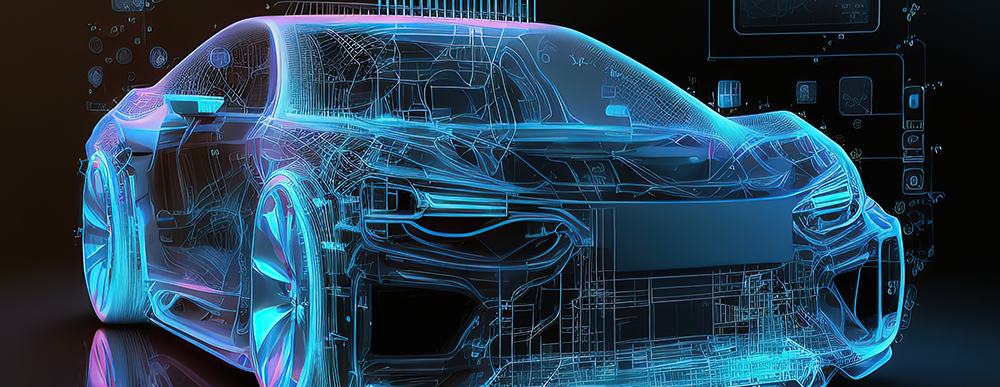
New high-strength industrial adhesives are currently being used in automotive and other manufacturing operations to replace spot welding, mechanical fasteners and other traditional joining methods. Adhesives offer several key advantages over traditional fastening technologies, including more uniform bond strength over a larger surface area compared to the localized strength typically achieved with mechanical fastening.
Adhesives and sealants are also used to join substrates or seal joints or gaps. They come in a variety of forms, but are usually dispersions containing polymeric materials or hardeners, surfactants and solvents. In the case of reactive adhesives, adhesion can be induced by mixing two or more reactive ingredients such as epoxy resin and hardener, or by external stimuli such as ultraviolet rays, heat, and moisture. In the case of non-reactive adhesives, adhesion is induced by a physical stimulus, for example pressure or solvent evaporation.
Most adhesives and sealants are composed of polymeric materials or contain monomers or oligomers that react to form cross-linked polymer networks. As a result, the molecular weight and molecular structure of these components are very important for the material properties before and after bonding. Many adhesive and sealant formulations are two-phase systems containing emulsions containing dispersed polymers or, in the case of caulk, dispersed solids. In both cases, particle size and droplet size can be critical to product performance.
The adhesive or sealant must flow to the substrate surface and then change from a flowable liquid to a structural solid without creating harmful internal stresses in the joint. Many adhesive or sealant problems that occur are not due to poor material selection or joint design, but are often directly related to poor production techniques lacking proper process control.